Shutdown optimization
Make sure your downtime is effective
Stick to your strategic plan
Stick to a budget
Use your resources efficiently
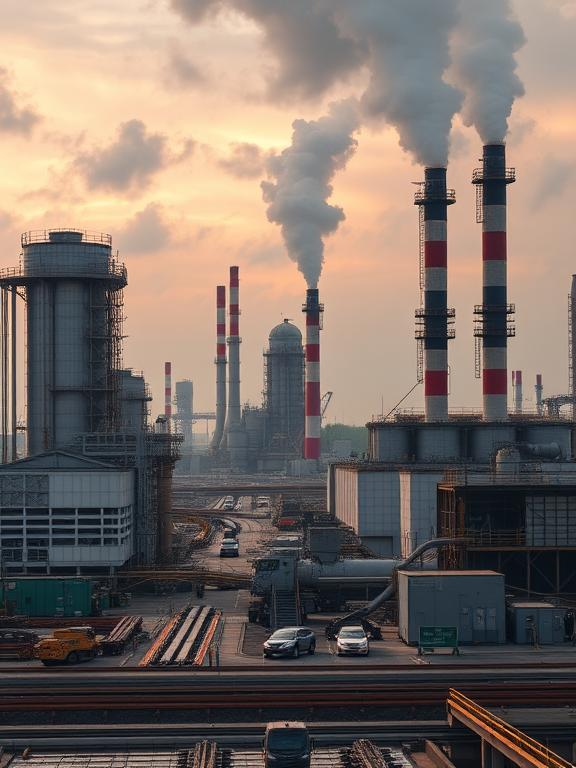
Customer downtime
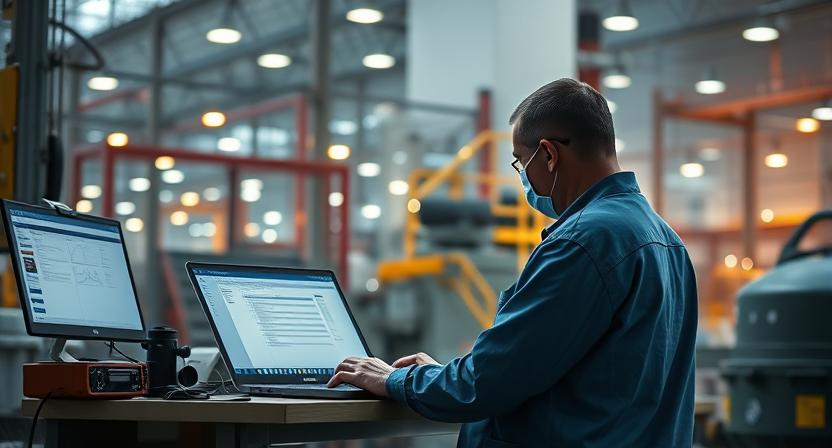
Setting steps
Are outages and shutdowns pushed close to the shutdown date?
Do you have extra work less than a week before your downtime? Are your downtime days chaotic?
You know that downtime is a key part of your success in achieving reliability and managing maintenance.
You probably already know why your downtime isn't working properly.
- But how do you get to a state of well-planned shutdown/turnaround?
- Can you get support from operations?
- Will the warehouse have the necessary parts?
- Are the checks that need to be performed completed before the shutdown?
We will help you implement effective planning and management of outages
Unify warehouses, operations, engineering and maintenance to successfully execute a common schedule.
Start and end the outage on time after all planned work is completed.
Avoid the stress and chaos of downtime by having the right people, tools and materials in place before the outage begins.
How Can We Help To Make Downtime More Efficient?
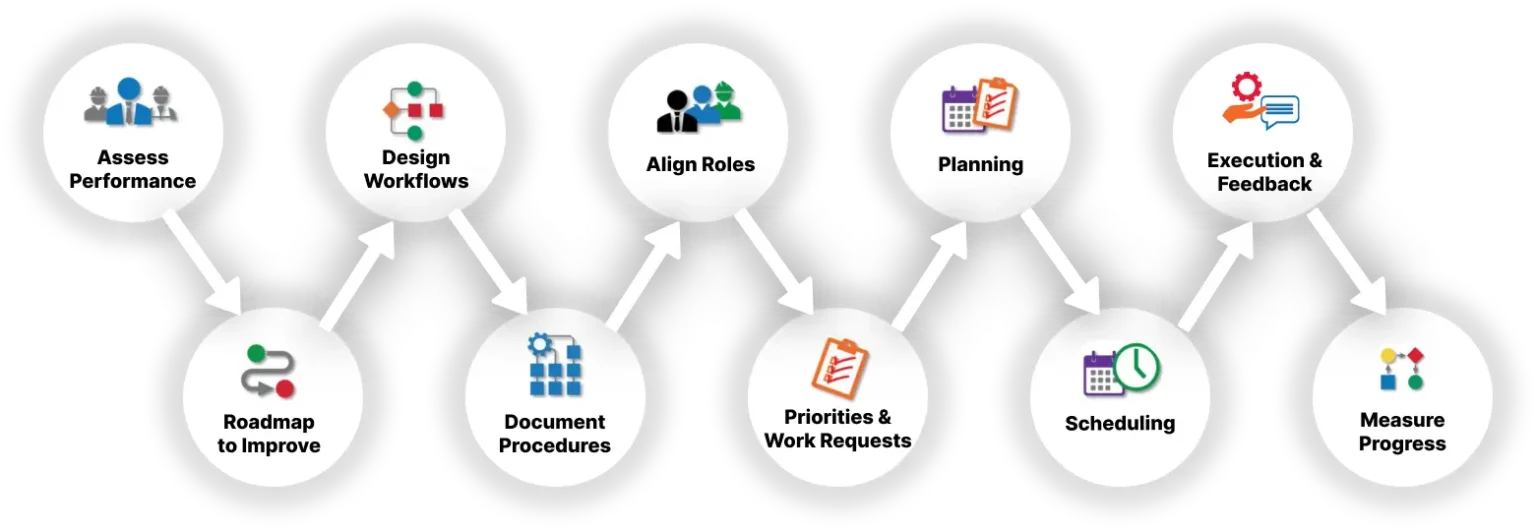
Start the shutdown with confidence
- Have an agreed upon start date for your schedule to create a plan to prepare
- Build teamwork to stick to the plan and be prepared with parts, tools, workflows, and coordination
- Gain confidence in your shutdown execution by staying on schedule, within budget, and completing the most critical tasks
Are you ready to make your team more efficient?